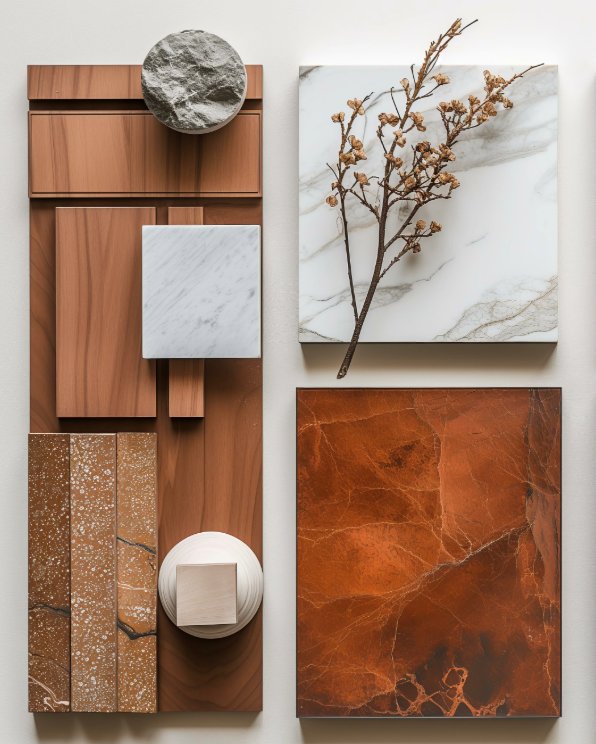
Design proposals
Space planning and layout design Interior design consultation Custom furniture design
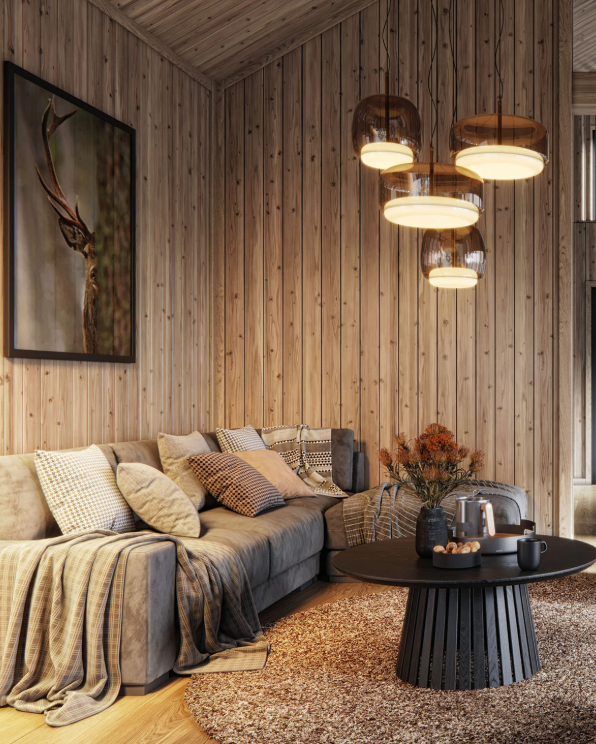
3D visualisations
GGIs 360 Animation

3D site scanning
Any size of room/public area All data import direct into computer
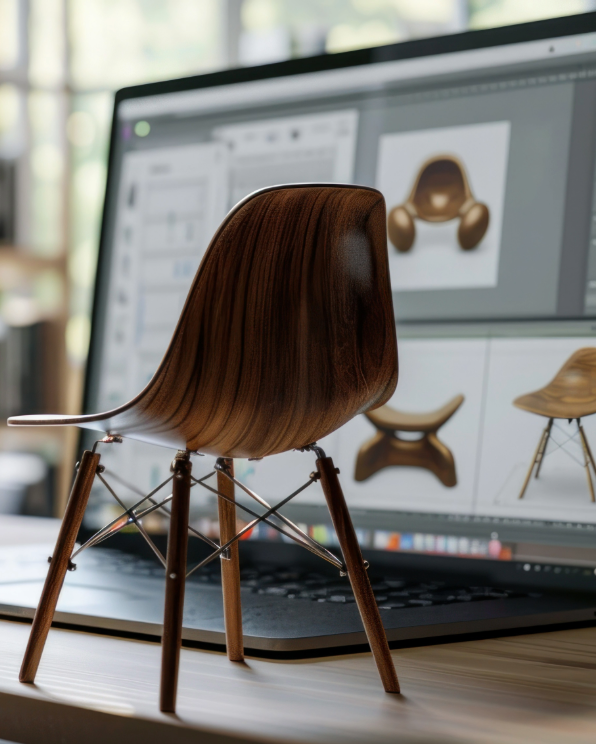
Value engineering
Enhancing project efficiency and quality Cost optimization Value maximization
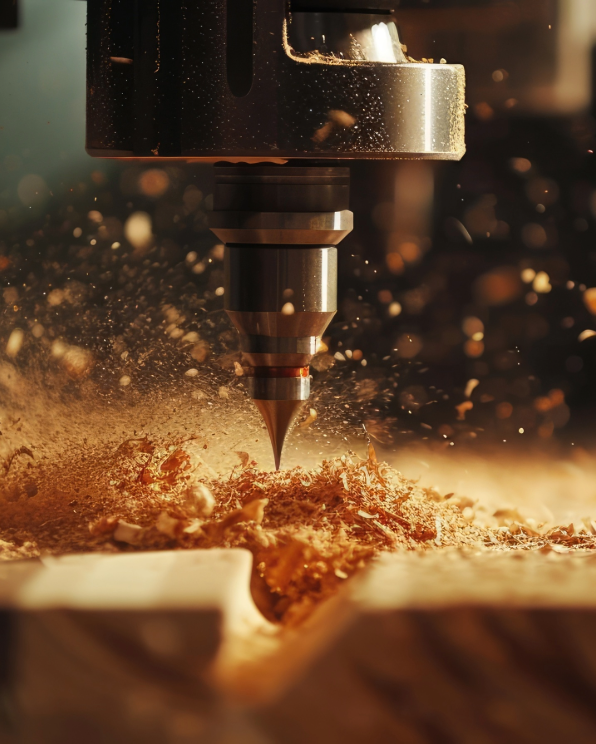
Production
Unique pieces by combining wood, stone, metal, brass, glass, and more for tailored, high-quality solutions Flexible due to multiple owned factories Complete oversight of quality and processes
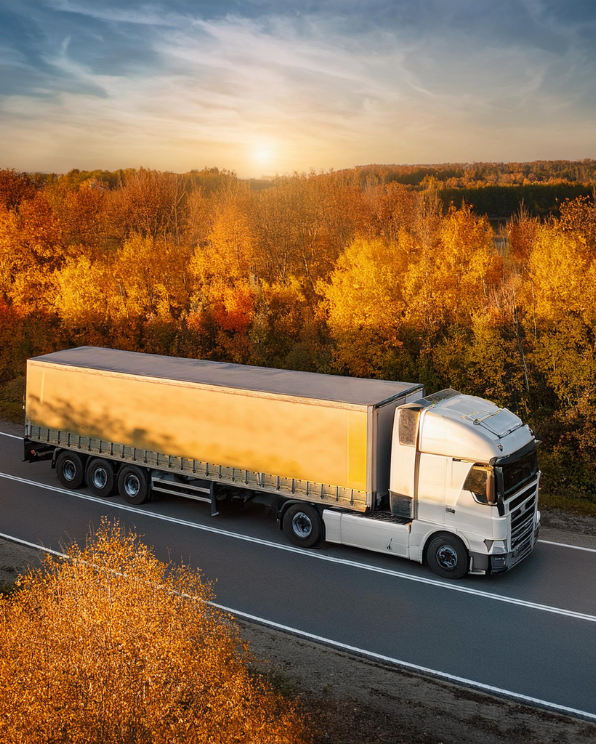
Logistics & delivery
Flexible truck sizes to accommodate all cargo needs Comprehensive handling of custom paperwork Delivery options via road, sea, and air
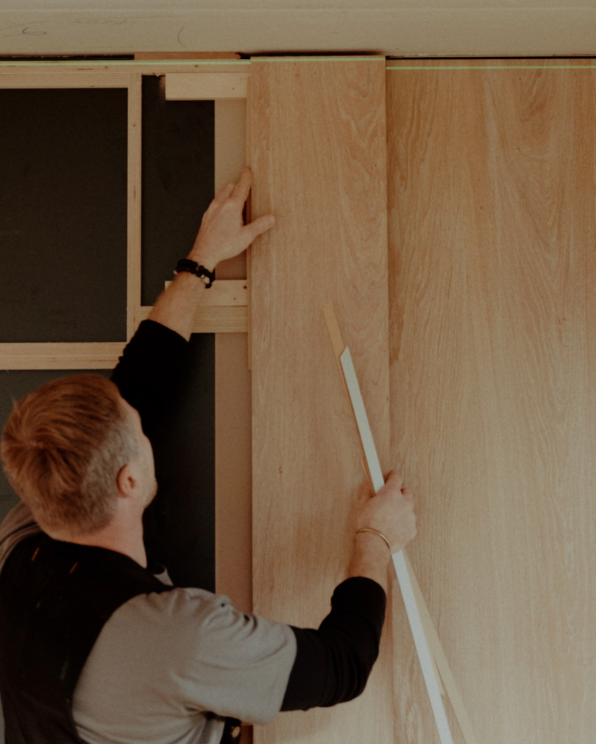
Installation
Scalable team sizes to meet project demands; English/German/French speaking site managers 24/7 online reports

Branded products supply
High-quality branded furniture selection Tailored solutions for every budget Efficient delivery and installation

Furniture refurbishment
Any type of furniture From new or reused materials Exceptional sustainability standards